There’s always a lot going on at any dock, primarily in the loading area. Trucks rushing in out and products being loaded and unloaded, pedestrians and forklifts – never a good mix – can make the environment unsafe for your staff. According to OSHA, there are about 85 fatalities involving forklifts every year and tractor-trailers are the second leading cause of backover fatalities in the US. Taking extra precautions around your dock site to ensure safety the of everyone is fundamental. Here at Ulti, safety is a priority so we’re here to give you our top tips on keeping everyone safe in your loading dock environment.
The basics:
There are some common knowledge safety tips that all your employees should be aware of when working at a dock loading site. Here are some basics that you can put around the site to reaffirm your workers.
- Wear sturdy non slip shoes to prevent injury
- Don’t run around the loading site
- Have good communication throughout the loading site and be aware of your surroundings
- Don’t mess around on site as it could result in injury to yourself or others
The safety measures:
Now the above basics are all well and good, but sometimes people just don’t pay attention to what they are doing or miscommunications can occur, which can potentially lead to disasters. So there are a few extra safety precautions that you can implement within your dock loading site to add peace of mind and mitigate any worst-case scenarios.
1. Drop-off zone safety barriers
As there is a gap between the loading site and the dock, this provides high risk for falls, where operating forklifts within the loading site can potentially fall off and injure both the operator and damage the forklift and your product. A way of preventing falls is by having a removable safety barrier like the Dok-Guardian Safety Barrier. This barrier can withstand huge force, preventing your forklifts from going over the edge, and are quickly and easily put in place, and then removed so loading can begin.
2. Protect your employees
Protecting your employees is extremely important, especially in an environment where there is a high risk of injury regarding vehicles and pedestrians. By placing Impactable barrier protection around zones designated for pedestrians, you are helping to prevent accidents that may occur. PVC impactable barriers are shock absorbent which helps to stop vehicles from penetrating through and hurting a worker.
When both pedestrians and forklift trucks share the same space, it is very important to have traffic lights.
The Safe-T-Signal Warning System detects traffic from all directions and communicates to oncoming traffic at intersections. It uses high-visibility traffic control LED symbols to signal a pedestrian/forklift to stop or yield. It also projects a blue LED light on the floor to signal workers that they are approaching an intersection.
3. Trailer Safety
Make sure to secure each trailer that comes onto your loading dock to prevent damage to any of the goods or those around the site, by using trailer restraints. The Global Wheel Lock restraint, automatically engages the rear tyre of the truck or trailer with a barrier, preventing the truck from moving away until it is released from inside the dock area.
Alternatively, a rear guard trailer restraint such as the Dok-Lok, uses a unique rotating hook design, to rotate upwards when the trailer is in position, to lock the trailer in place. These restraints can be integrated into the controls inside the building meaning the truck can not move away until all is safe.
Vehicle restraints should not only secure a trailer to the building but also provide danger notifications. Hazard recognition and communication to pedestrians and material handling operators can be done using the Rite-Vu™ Hazard Recognition and Light Communication System.
4. Trailer Support
A trailer collapsing could cause major damage and risk injury to your workers, that is why stability is key when unloading goods off trailers. Adjustable trailer stabilisers or trailer stands should be placed under trailers to give them the extra support they need when you are loading or unloading goods.
5. Alert both pedestrians and traffic
Awareness is a big safety factor, especially in a busy loading dock site. There are multiple ways that you can create this awareness for both the pedestrians around the site and the trucks coming onto the site. Approach-Vu signals to pedestrians through visual and audible warnings to alert that there is a vehicle reversing on the site. Pedestrian-Vu detects inside trailer activity and warns oncoming traffic with a blue flashing light.
With Dock Light Communication Systems, simple red and green traffic lights help dock workers inside your building communicate with truck drivers outside, improving both safety and productivity at your docks. These lights can be both external for the truck drivers, as well as internal, so it can be easily seen that a certain dock is open and safe to enter the trailer. Clear, concise communication to the right person, at the right time, in the right location.
6. Adequate Preventive Maintenance
A regular preventive maintenance program for loading dock equipment including dock levellers, restraints, doors, dock bumpers, lights, and communication systems must be established.
Ensure that good housekeeping practices are in place. Clean up spills and leaks immediately and remove and dispose of any packaging materials (cardboard, pallets, plastic, etc.). Regularly check dock seals and shelters to ensure they are not leaking. Minimise worker exposure to vehicle exhaust and temperature extremes, as well as minimise deterioration of the building envelope due to weather.
Keep your dock loading area free from contamination during loading and unloading using a Dock Seal that effectively seals off the smallest of gaps and take the harshest of impacts. Read more on Dock Seals & Shelters
Want to know more about how you can make your loading dock safe? Contact our customer service team today!
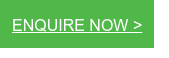